Where is your safety culture heading?
- Dec 16, 2022
- 7 min read
Updated: Dec 19, 2022

By Norman Halverson
Decades ago, my son won an award for writing a short story and received an invitation to attend a conference for young writers. At the conference, the keynote speaker was a successful author who discussed the evolution of his creative process with the group of young writers and their parents. As I struggled to remain interested in hearing about his life story and the creative literary process he used, one piece of advice caught my attention and has stuck with me for all these years. He explained that after several drawn-out attempts to write his first few books, his efforts continually felt like a battle to complete his work in a reasonable amount of time. After completing the initial draft, the editing process required constant changes to both the story and the ending, just so everything would make sense and come together at the end of the book. He was “winging it” and always putting out fires along the way in hopes of having a quality product when it was finally completed. Very frustrating and inefficient!

After researching various creative methods, the author decided to change his approach by writing the ending of his story first, and then developing the characters and story line that aligned with the ending. He summed up his process change with a simple question: “how will you know you’ve reached the destination if you don’t know what it is?” He described how much easier the creative process became after already knowing how the story would end. This new approach resulted in a more structured process that kept his focus on the critical items that were necessary and important to reach the end of the story. With practice, the creative process itself became more systematic and contrasted sharply to the original approach of writing with no idea where the story was going, and then trying to piece it all together at the end. By beginning his process with the ending in mind (vision), the author laid the foundation for a more structured and predictable work process, which ultimately led to his ability to produce higher quality books in less time.
How does this story relate to safety culture?
As we know, a company’s operating culture has a tremendous amount of influence on employee and manager behaviors as it relates to safety in the workplace. When looking at your culture through the professional safety lens, do you honestly know where your company is heading? Are you constantly shooting from the hip and reacting to safety issues as they arise? Do you have a true understanding of what best-in-class safety looks like? Has the leadership team established a vision for achieving the safety excellence your employees and company deserve?
Having an unclouded vision of safety excellence before installing any kind of safety management tools, systems or best practices will create the foundation to develop a more focused improvement process, which will produce superior results in less time than it takes to “wing it.” As part of your journey, a proper gap analysis and needs assessment will identify the necessary tools, systems, and best practices because they will be in alignment with your vision of the future state. Without a clearly defined vision of "who we are" as it relates to company safety culture, you will often find yourself in a reactive state that is costing your business much more than you realize when it comes to human and financial capital.
The idea here is to instill safety as a core value, rather than just being a priority that can (and does) change in an instant. Developing your vision of safety excellence will lay the foundation for a value-based approach that defines the desired cultural goals and provides the structure needed to holistically build the tools, systems, and best practices necessary to achieve safety excellence.
This may appear to be common sense and somewhat obvious, however, there are many of us out there who become caught up in putting out fires each day and lose sight of the big picture. When a safety event occurs, our problem-solving instinct immediately kicks in and we jump into action to fix the issue. At times we may even dig a little deeper to address process level issues, however, deeply rooted contributing factors associated with poor, inadequate or misguided cultural beliefs are commonly overlooked because they have not been established as expectations and values.
Without a clearly defined vision of "who we are" as it relates to company safety culture, you will often find yourself in a reactive state that is costing your business much more than you realize when it comes to human and financial capital.
Establishing a value-based cultural vision for safety also delivers a heightened level of expectations and criteria when conducting any kind of root cause analysis exercise. Whether you are performing an incident investigation, FMEA, kaizen event, or Lean/Six Sigma project, it is critical to review potential causal factors from a cultural perspective, rather than just a process level perspective. By excluding the contributing cultural factors in the process or incident review, you may be leaving untapped improvement opportunities on the table and negatively impacting your long-term injury rates and associated costs.
Common values associated with best-in-class safety culture
Undoubtedly, you've heard about companies having best-in-class safety cultures and wondered how they attain such a level of success. What is the secret sauce that helped them achieve safety excellence? Simply put, these companies decided that safety should be a core value and then built the appropriate programs to achieve that vision.

Organizations achieving best-in-class safety often come from a variety of industries with dissimilar operations and processes. Nevertheless, there are parallels in the beliefs, values and expectations they used to craft a safety culture vision that led them to attaining best-in-class status. These companies did not have all the answers in the beginning of their journey to safety excellence. However, their vision built the foundation to integrate effective management systems, tools, and best practices into daily operations, leading them down the path towards safety excellence.
Below are core values, beliefs, and philosophies commonly shared by companies considered to be best-in class for safety:
· Injuries are considered preventable and predictable
· Regulatory compliance is not good enough
· Continuous improvement is required
· We are proactive, not reactive
· Operational departments own the responsibility for safety
· Safety is every employee’s job
· Safety is a strategic business initiative
What is your vision of safety excellence?
As you consider the information being discussed, keep in mind this concept differs from the framework elements you will find in OSHA VPP or the ISO 45001 safety management systems. These common core values should be thought of as “this is who we are” statements, not “this is how we do it". The key elements involved in the VPP, and ISO programs become the "this is how we do it" part of the evaluation, planning, and execution phases, after the vision is established. Safety excellence is a never-ending journey that requires layers of systems, tools, and best practices that collectively result in a holistic approach to building a strong culture. That said, it all starts with an unclouded vision of what safety excellence looks like up front, so you can maintain proper focus on the vision.
As previously mentioned, company culture significantly influences the behaviors of the entire leadership team and the employees, especially when it pertains to managing safety within the operational departments. Generally speaking, safety people work diligently towards reducing risk and have a passion for what they do, but they often can’t change the culture of an entire company alone. The larger and more complex the organization, the greater the challenge.
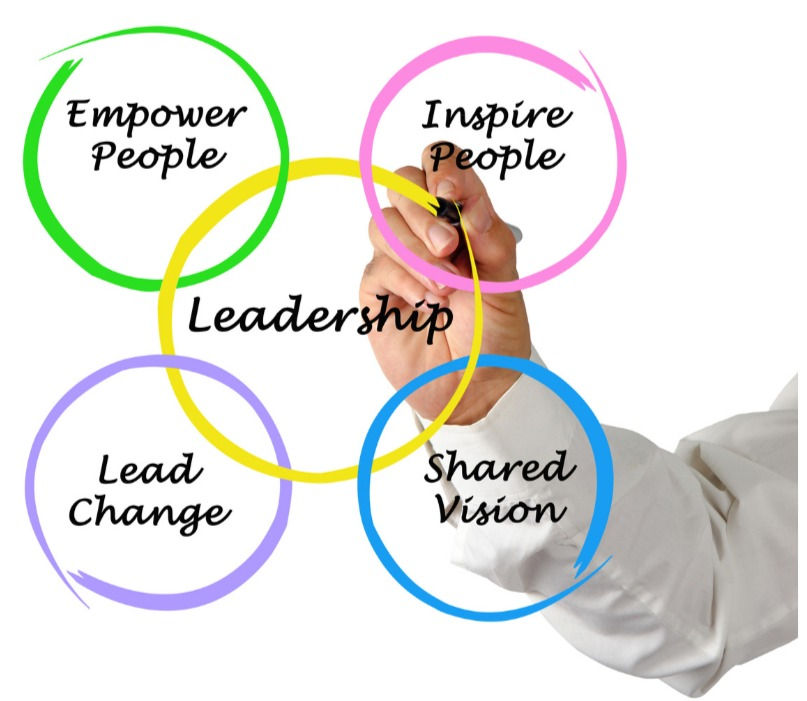
Company leadership owns the responsibility for facilitating the development and maintenance of safety culture. However, this exercise in continuous improvement should be a team effort and not just mandates emanating down from the corporate office. It is imperative that leadership includes safety personnel and non-management employees in the process of creating a safety culture vision your employees and business deserves. Without a clear vision and path to excellence, your company will struggle to reach its full potential, which can have lasting negative effects on the employee population as well as the business itself.
I believe nearly everyone can understand the importance of improving safety as it relates to the employees, however, one example of how your business can benefit comes from the last bullet point in the above list. If leadership is open to the idea of safety excellence being a strategic element of business planning, your improvement journey will begin to uncover benefits that may not have been previously realized. Research shows that investing in safety often pays a 3-5x return, and for public companies, there have been strong correlations between safety excellence and improved stock price. In fact, best‐in‐class firms commonly have higher relative market valuations than industry peers with lower levels of safety performance. Employee morale, productivity and efficiency are also known to improve as the company culture heads down the path to safety excellence.
Company leadership owns the responsibility for facilitating the development and maintenance of safety culture
In summary, your journey to safety excellence starts with a vision of what best-in-class safety should look like for your business. If you truly feel that human capital is in fact the company's greatest asset, then your safety vision should be an unwavering set of core values that steadfastly drives the behaviors of managers and employees alike in the workplace.
This vision will lay the foundation for developing targeted management systems, tools, and best practices that integrate safety into day-to-day operations, and results in a culture where safety benefits both the employees, and the business.
Look for future articles that dive deeper into details on how to build your foundation to achieve safety excellence.
I really appreciate your time today.
Thank you for reading.
Safety Norm

With over 20 years of experience, Norm has a proven history of transforming safety culture in companies of all sizes by influencing key stakeholders and employing a forward-thinking approach to risk reduction.
Norm holds M.S. & B.S. degrees in Occupational Health and Safety from Columbia Southern University and is a certified Lean/Six Sigma Greenbelt.
For more information on building a culture of safety excellence, click on the following links:
OR
Email Norm directly to schedule a complimentary initial consultation:
Comments